ABSTRACT
The paper reports on temperature behavior of strain sensitivity of recently introduced screen printing technology facilitating the realization of silver and carbon black piezoresistors embedded in organic coatings. Piezoresistive layers were prepared by screen printing directly on the top of the organic coating. Since no glue or carrying substrates are between the sensitive element and the device under test, the coupling factor is high and the strain is efficiently transferred to the sensing element.
The strain induced changes in resistance (piezoresistive effect) are generally lower compared to the changes induced by temperature. The temperature dependence of the sensitivity to strain was investigated utilizing both single element piezoresistors and piezoresistors connected to a Wheatstone bridge. The study analyzes strain-gauges under longitudinal tensile and compressive strain and temperatures up to 80°C. Screen printed strain gauges can provide reliable and robust strain measurements for coated metallic substrates, the sensor performance is comparable to the conventional solution with glued sensors.
MATERIALS AND METHODS
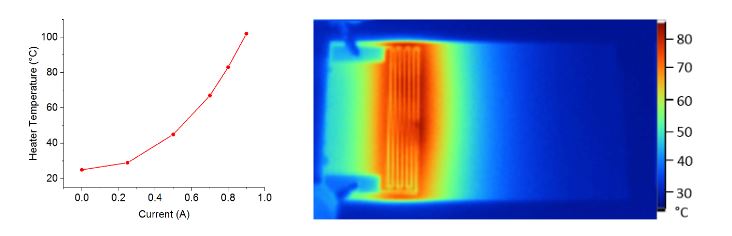
Figure 1. Heating curve and IR image of screen printed silver heater
A strain gauge array was printed on top of a coated steel substrate. The heater, which is used for temperature characterization is printed underneath on the bottom side of the substrate. The heater covers the area of the sensor array to achieve a uniform temperature distribution along the sensor array (see Figure 1). The screen printed heater is capable of heating the substrate (130 × 70 × 0.6 mm 3) up to 100°C at a power of 25 W. The stability of the surface temperature (on the sensor side) was measured using a PT1000 temperature sensor in an SMT0603 package.
RESULTS
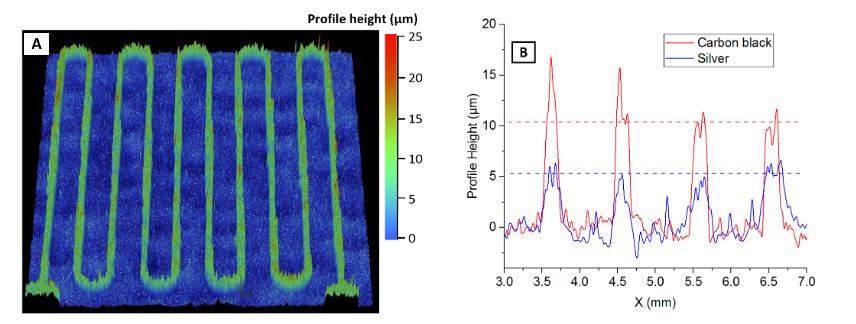
Figure 3. 3D scan (A) and printed line profiles of the silver and carbon black sample (B) with line width of 200 μ m
Realized structures were scanned with a Bruker Dektak XT profilometer. The measured profiles depicted in Figure 3 show that final thicknesses of the sensitive layers are ~5 μ m and ~10 μ m for silver and carbon black respectively (a 120/34 threads/inch screen printing mesh was used).
CONCLUSIONS
The results show that, while the strain sensitivity of silver paste is constant over the measured temperature range (gauge factor GF ~1.8), the sensitivity of carbon black has increased in the measured temperature range from 0 to 80°C (GF 4.1 ÷ 5.8). In both cases, the electrical conductivity originates from conductive paths within the polymer matrix, and the piezoresistive behavior is influenced by both intra- and inter-particle effects.
The resulting strain sensitivity depends on factors like particle conductivity, percolation level and process parameters (e.g., curing temperature). Silver strain gauges exhibits excellent linearity, repeatability and constant temperature coefficient of resistance over wide range of temperatures. Carbon black exhibits a higher deformation sensitivity (GF is 2 ÷ 3 × higher, compared to silver), but its temperature dependence of deformation sensitivity is also high er and disadvantageous in the practical utilization and design of conditioning circuits.
Source: Johannes Kepler University
Authors: Pavel Kulha | Herbert Enser | Johannes K. Sell | Bernhard Straus | Michaela Schatzl-Linder | Bernhard Jakoby | Wolfgang Hilber