ABSTRACT
Using piezoresistive pressure sensors and in situ measurement of pressure gradient, the infusion of resin in fiber reinforced composite can be optimized. The optimization of resin flow in Vacuum Assisted Resin Infusion (VARI) is necessary to produce high-quality fibre-reinforced composites. To control the resin infusion process, piezoresistive pressure sensors are embedded to detect the resin flow and resin pressure in Carbon Fibre Reinforced Polymer (CFRP). The measured pressure validates the accuracy of analytical calculations, based on Darcy’s law in a porous medium. The sensors are of small size and therefore do not affect the natural flow of the resin.
MATERIALS AND METHODS
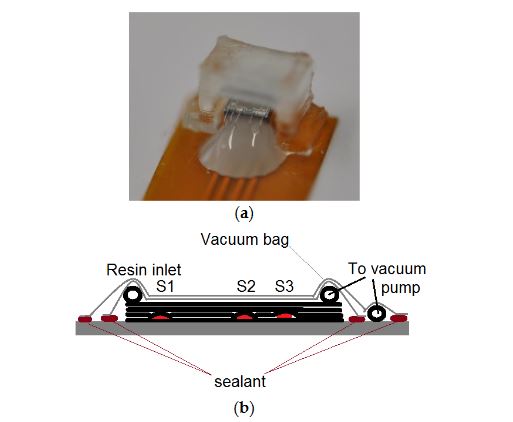
Figure 1. (a) A piezoresistive pressure sensor wire bonded on a Kapton PCB
Three piezoresistive pressure sensors are embedded on the bottom ply of the 4-layer carbon fabrics laminate. The stacking of fibers and sensors are schematically shown in Figure 1b. The sensors are placed with a distance of 2.8, 13.0 and 31.0 cm from the infusion line. Spiral tubes are used to provide linear resin infusion and vacuum suction. The laminate is sealed and evacuated by a vacuum pump.
RESULTS AND DISCUSSION
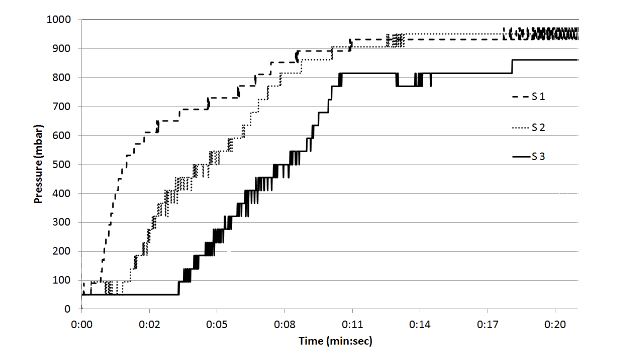
Figure 2. Measured pressure during resin infusion by pressure sensors. The laminate is filled up with the resin in 21 min
The resin reservoir is placed at atmospheric pressure. When the resin is infused into the laminate, pressure elevates gradually at the point impregnated by the resin. The sensor close to the resin infusion point shows faster changes in pressure than others. Figure 2 demonstrates the measured pressure inside the laminate during the resin infusion. When the resin reaches any of the embedded sensors, that sensor measures a sudden increase in pressure.
Source: University of Twente
Authors: Maryam Kahali Moghaddam | Arne Breede | Adli Dimassi | Walter Lang