ABSTRACT
An aluminum nitride (AlN) based patch antenna-type high-temperature wireless passive sensor is reported to operate as both a sensor and an antenna, which integrates in situ measurement/sensing with remote wireless communication at the same time. The sensor is small, easy to manufacture, highly sensitive and has a high operating temperature; it can be used in high-temperature, chemically corrosive and other harsh environments.
The sensing mechanism of the sensor, the dielectric constant of the AlN ceramic substrate, increases with rising temperature, which reduces the resonant frequency of the sensor. Thus, the temperature can be measured by detecting changes in the sensor’s resonant frequency. High-Frequency Simulation Structure (HFSS) software is used to determine the structure and size of the sensor, which is then fabricated using thick-film technology. The substrate of the sensor is AlN ceramic due to its outstanding thermal resistance at high temperature; and its conductors (the radiation patch and the ground under the substrate) are silver-palladium alloy sintered form silver–palladium paste.
A vector network analyzer reveals that the sensor’s operating range extends to 700◦C. Furthermore, its resonant frequency decreases from 2.20 GHz to 2.13 GHz with increasing temperature from room temperature (25◦C) to 700◦C, with an absolute sensitivity of 104.77 KHz/◦C. Our work verifies the feasibility of measuring high temperatures using AlN-based patch antenna wireless passive temperature sensors, and provides a new material and temperature sensitive structure for high-temperature measurement in harsh environments.
MEASUREMENT PRINCIPLE
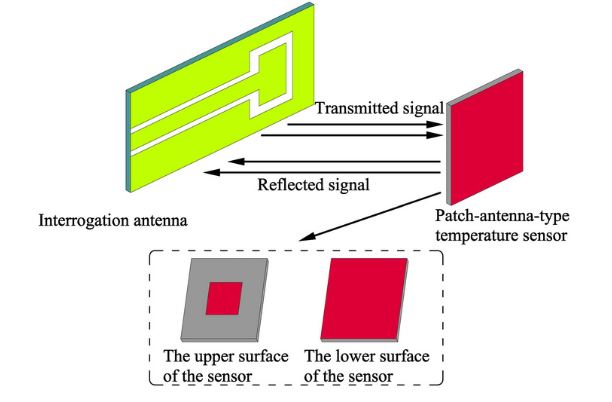
Figure 1. Schematic diagram of the patch antenna temperature sensor system
Figure 1 shows the schematic diagram of the patch antenna-type wireless passive temperature sensor system, which consists of a temperature sensor and an interrogation antenna. The temperature sensor is a resonant patch antenna consisting of an AlN ceramic substrate with a metal patch on its upper surface and a metal ground on its lower surface. An Al2O3-based patch loading slot antenna is used as the interrogation antenna, and a coplanar waveguide feed is adopted. To sense the temperature, the antenna sends a sweep signal with a certain bandwidth to the temperature sensor.
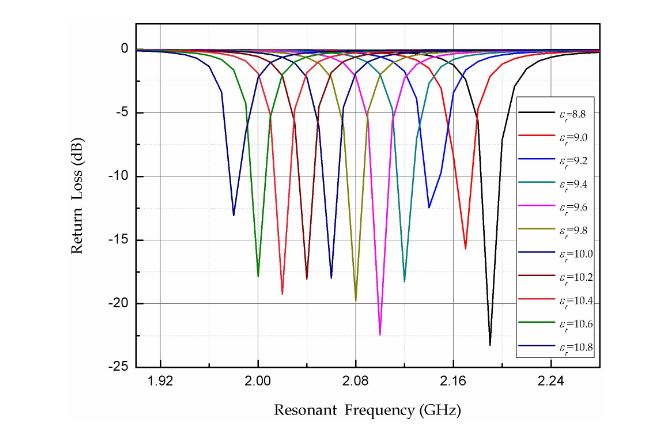
Figure 3. Simulated S11 curves of the sensor for different dielectric constants of the aluminum nitride (AlN) ceramic material
Figure 3 shows S11 curves corresponding to different dielectric constants of the AlN substrate. The trough of the S11 curve corresponds to the resonant frequency of the sensor. Obviously, as the dielectric constant of the AlN substrate changes, the resonant frequency of the sensor changes. For a clearer view of the relationship between the resonant frequency of the temperature sensor and the dielectric constant of the material, the valley points in Figure 3 are extracted and plotted as a curve, as shown in Figure 4. The resonant frequency clearly decreases as the permittivity increases. Therefore, the principle of the sensor is verified.
TEMPERATURE SENSOR DESIGN
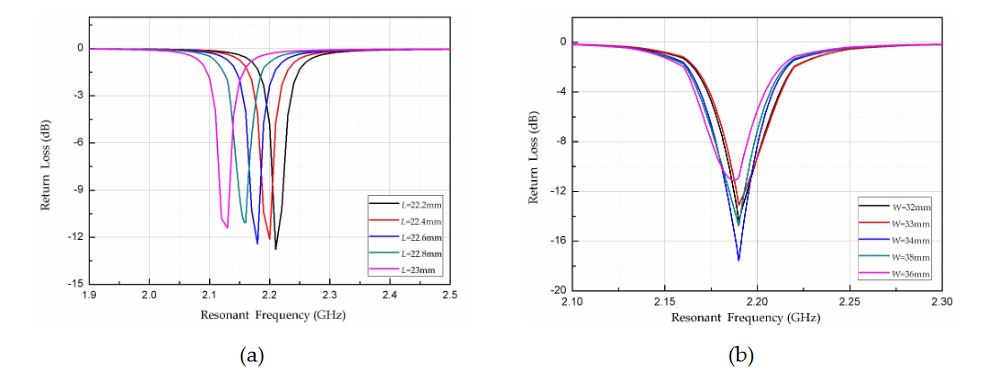
Figure 5. High-frequency simulator structure (HFSS) simulation results: (a) length L; and (b) width W of radiation patch
According to formulas (3), (4) and (5), the radiation patch length of the temperature sensor L is 22.9 mm. To improve the radiation efficiency of the sensor and reduce the reflection and transmission losses, the length L and width W of the sensor radiation patch were optimized on the basis of the theoretical value obtained using HFSS, as shown in Figure 5. The resonant frequency fr of the sensor decreases gradually with increasing length of the radiation patch.
TEMPERATURE SENSOR FABRICATION
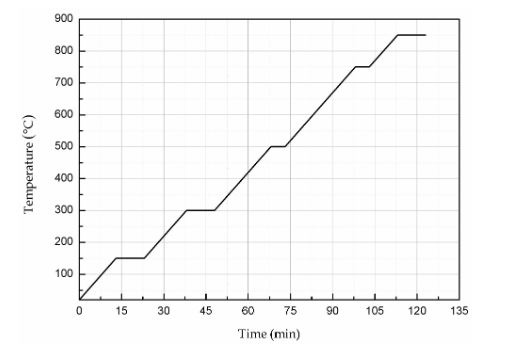
Figure 6. Sintering curve of the silver–palladium slurry
The thickness of the radiation patch is 25 μm, much larger than the calculated value of the skin depth, so the effect of the skin effect can be neglected. After the printing was completed, the silver–palladium metal paste was sintered to solidify it and form a dense metal layer on the surface of the ceramic substrate. During the sintering process, the temperature was raised from room temperature (20◦C) to 850◦C at a rate of 10◦C/min for 123 min and then cooled naturally to room temperature. Figure 6 shows the sintering curve.
MEASUREMENT AND DISCUSSION
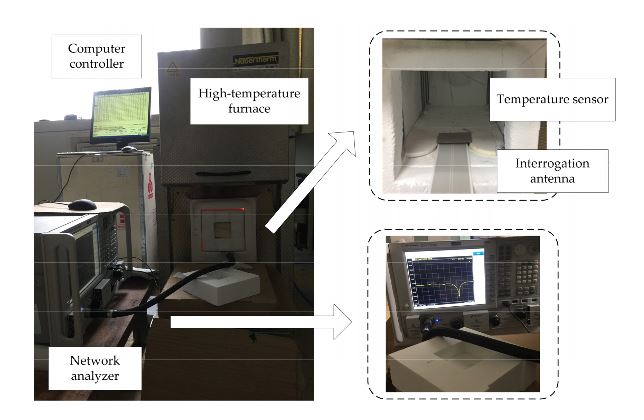
Figure 9. Temperature testing setup
During the heating process, the temperature was increased at a rate of 10◦C/min; and when the temperature had changed by 100◦C and held for 10 minutes, the experimental data were recorded. In the testing system, high-temperature insulation material 50 mm thick was installed in the door of the furnace to improve the accuracy of the temperature and reduce the heat loss.
Inside the furnace, the temperature sensor was placed parallel to the front of the interrogation antenna at a distance of 15 mm. The testing setup is shown in Figure 9. Micromachines 2017, 8, x 8 of 13 the furnace to improve the accuracy of the temperature and reduce the heat loss. Inside the furnace, the temperature sensor was placed parallel to the front of the interrogation antenna at a distance of 15 mm. The testing setup is shown in Figure 9.
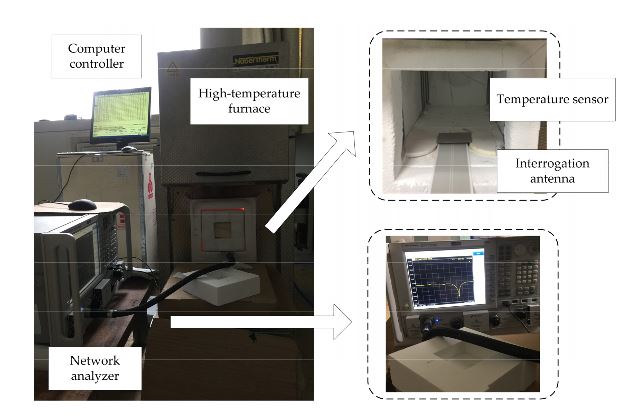
Figure 14. Sensor repeatability test curve: (a) heating process; (b) cooling process
Using the same test system, the sensors were tested three times to verify the repeatability during heating and cooling. The valley points were extracted from the heating and cooling curves and are plotted in Figure 14a,b, respectively. Below 400◦C, the sensor exhibits very good repeatability, as the curves overlap almost completely. Therefore, the AlN-based patch antenna temperature sensor has excellent practical utility and test reliability below 400◦C.
CONCLUSIONS
This paper presents a patch antenna-type wireless passive temperature sensor made of an AlN ceramic material and silver–palladium metal paste. The sensor has advantages such as high-temperature operation, compactness, a simple structure, ease of processing, ease of integration, and low cost; furthermore, it can be applied in harsh high-temperature environments. The feasibility of applying an AlN material and a thick-film printing process to sensors for high-temperature measurement is proved by theoretical analysis, simulation, fabrication, and experiment.
The resonant frequency of the sensor changes from 2.20 GHz to 2.13 GHz as the temperature is raised from room temperature (25◦C) to 700◦C, and the absolute sensitivity is 104.77 KHz/◦C. Three measurements during heating and cooling were performed and showed that the sensor has good repeatability below 400◦C and a small hysteresis error. Our future work will improve the sensitivity and sensing distance of the sensor by improving the fabrication process and machining accuracy and designing a high-gain broadband interrogation antenna.
Source: North University
Authors: Dan Yan | Yong Yang | Yingping Hong | Ting Liang | Zong Yao | Xiaoyong Chen | Jijun Xiong
>> Antenna Projects Using HFSS for ECE Final Year Students
>> Antenna Signal Processing Projects for Engineering Students