ABSTRACT
The demand for batteries for energy storage is growing with the rapid increase in photovoltaics (PV) and wind energy installation as well as electric vehicle (EV), hybrid electric vehicle (HEV) and plug-in hybrid electric vehicle (PHEV). Electrochemical batteries have emerged as the preferred choice for most of the consumer product applications. Cost reduction of batteries will accelerate the growth in all of these sectors. Lithium-ion (Li-ion) and solid-state batteries are showing promise through their downward price and upward performance trends.
We may achieve further performance improvement and cost reduction for Li-ion and solid-state batteries through reduction of the variation in physical and electrical properties.These properties can be improved and made uniform by considering the electrical model of batteries and adopting novel manufacturing approaches. Using quantum-photo effect, the incorporation of ultra-violet (UV) assisted photo-thermal processing can reduce metal surface roughness. Using in-situ measurements, advanced process control (APC) can help ensure uniformity among the constituent electrochemical cells.
Industrial internet of things (IIoT) can streamline the production flow. In this article, we have examined the issue of electrochemical battery manufacturing of Li-ion and solid-state type from cell-level to battery-level process variability, and proposed potential areas where improvements in the manufacturing process can be made. By incorporating these practices in the manufacturing process we expect reduced cost of energy management system, improved reliability and yield gain with the net saving of manufacturing cost being at least 20%.
PROBLEM DEFINITION
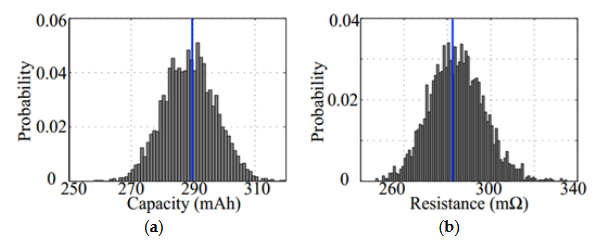
Figure 1. Probability distribution of the (a) cell capacity and (b) resistance profile of the sample cells.
Figure 1 shows a statistical distribution of cell performance for Li-ion cells in terms of capacity and resistance. The desired statistical distribution of the cell capacity in Figure 1 should have (a) a mean centered at higher value, i.e., the mean should move right, and (b) have a smaller (narrower) variation. Similarly, the statistical distribution of resistance should have (a) smaller mean value, i.e., move towards left, and (b) have a smaller (narrower) variation.
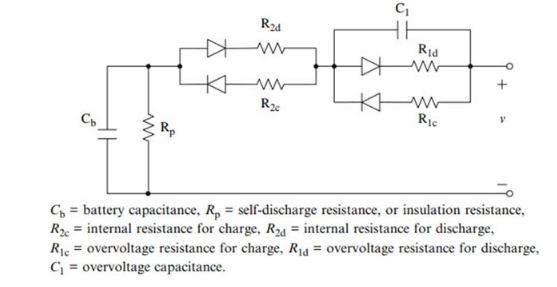
Figure 4. Equivalent circuit model of a battery
In a study carried out on solid-state electrolyte for Li-ion cells, the researchers concluded that variation in the cooling rate results in variation of ionic conductivity. Therefore, the thermal process needs to be controlled precisely to keep cooling rate consistent in all batches. The improvement in battery technology can come from utilizing the insight gained from the equivalent circuit model of the battery proposed.
Young et al. included battery capacitance (Cb), self-discharge resistance ( Rp ), internal resistance for charge ( R2c ), internal resistance for discharge ( R2d ), over-voltage resistance for charge ( R1c ), over-voltage resistance for discharge ( R1d ) and over-voltage capacitance ( C1 ). The equivalent circuit of Figure 4 provides a simple guideline for uniformity which dictates that when connecting more than one cell to form a battery pack, the contributing cells need to have the same values of Cb, R p, R 2c, R 2d, R 1c, R 1d and C1.
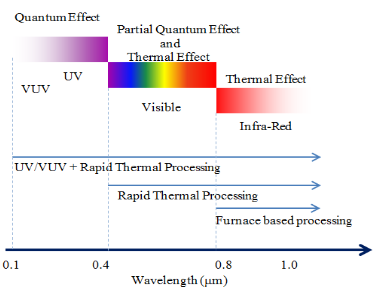
Figure 6. Radiation spectrum distribution for thermal processing techniques
A detailed mechanism of operating principles of RTP can be found. The photon-matter interaction can be summarized by the simple expression: “photon + matter = thermal effects + quantum effects”. The wavelength of photon dictates the degree of thermal and quantum effects in RTP. The effects of different wavelengths in RTP are illustrated in Figure 6. The typical radiation spectrum of furnaces operating in temperatures less than about 1500◦C lies in the infrared region.
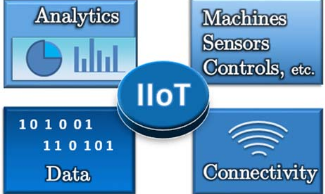
Figure 7. Industrial internet of things (IIoT) framework that utilizes connectivity, data, and analytic tools to communicate effectively with machines.
As shown in Figure 7, the incorporation of IIoT can provide business critical information that can prove to be crucial in manufacturing of products. In battery manufacturing, the materials are to be sourced from different vendors and the finished products are distributed through distributors or sold to customer companies. IIoT can significantly influence the supply chain.
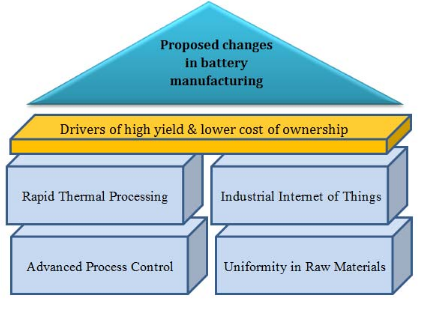
Figure 8. Proposed changes and their impact to bring down cost of ownership (COO).
The steps proposed in this paper would increase the throughput, yield and material utilization and decrease the battery manufacturing cost, due to higher yield. Thus, the net result will be reduction of COO. With incorporation of all the proposed changes, we expect to manufacture higher quality batteries at a cheaper cost. All the proposed changes are presented in concise graphical form in Figure 8.
CONCLUSION
Process variation in manufacturing is one of the key factors that reduces optimal battery performance and leads to higher manufacturing cost. There is room for improvement in controlling the process variations observed in battery manufacturing. In this paper, we have emphasized that the variation from cell-to-cell is crucial for energy storage application. The SPC used currently by battery manufacturers should be replaced by APC to gain better control over the manufacturing process. The use of RTP in place of CFP is suggested in all thermal process steps to reduce process variability and improve the performance and reduce cost of batteries.
IIoT has the potential to manage manufacturing in a more efficient and agile manner. Besides research in materials and chemistry, these steps can help a manufacturer to produce in an efficient way while delivering the best quality product. The battery industry needs to act quickly to be prepared for the future when battery storage plays a very important role in stationary applications for power storage, as well as in EVs used in the surface transport sector.
Source: Clemson University
Authors: Amir A .Asif | Rajendra Singh
>> 200+ IoT Led Projects for Final Year Students