ABSTRACT
Complex and customized manufacturing requires a high level of collaboration between production and logistics in a flexible production system. With the widespread use of Internet of Things technology in manufacturing, a great amount of real-time and multi-source manufacturing data and logistics data is created, that can be used to perform production-logistics collaboration. To solve the aforementioned problems, this paper proposes a timed colored Petri net simulation-based self-adaptive collaboration method for Internet of Things-enabled production-logistics systems. The method combines the schedule of token sequences in the timed colored Petri net with real-time status of key production and logistics equipment.
The key equipment is made ‘smart’ to actively publish or request logistics tasks. An integrated framework based on a cloud service platform is introduced to provide the basis for self-adaptive collaboration of production-logistics systems. A simulation experiment is conducted by using colored Petri nets (CPN) Tools to validate the performance and applicability of the proposed method. Computational experiments demonstrate that the proposed method outperforms the event-driven method in terms of reductions of waiting time, makespan, and electricity consumption. This proposed method is also applicable to other manufacturing systems to implement production-logistics collaboration.
FRAMEWORK
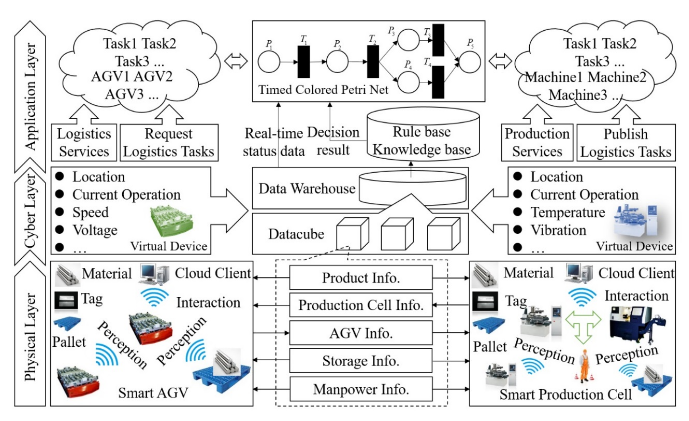
Figure 1. An integrated framework based on cloud service platform for production-logistics systems. AGV: automated guided vehicle.
In order to solve the aforementioned problems, an integrated framework based on a cloud service platform for production ‐ logistics systems is introduced as shown in Figure 1. The proposed framework is composed of three layers, namely the physical layer, the cyber layer, and the application layer. The aim of this framework is to provide the foundations for production ‐ logistics collaboration.
- The Physical Layer
- The Cyber Layer
- The Application Layer
METHOD
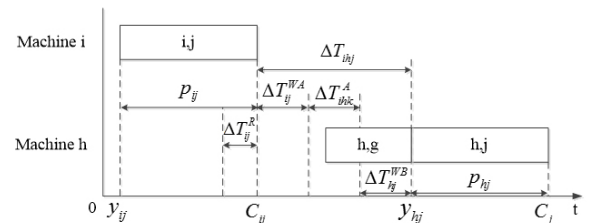
Figure 2. The simplified schedule plan of a job
Assuming that a feasible schedule plan is given as in Figure 2, first, the job j is processed on the machine i. The starting time of operation ( i , j ) is yij. The processing time of operation ( i , j ) is pij. The completion time of operation ( i , j ) is Cij. The remaining time of operation ( i , j ) is ∆TRij. Then, after the operation ( i , j ), the WIP is transported to the next machine h. The waiting time between operation ( i , j ) and operation ( h , j ) is ∆Tihj.
The waiting time of the job j on machine i before processing is ∆TWBij. The time cost of AGV k going from machine i to machine h is ∆TAihk. The waiting time of the job j on machine i after processing is ∆TWAij. Next, the job j is processed on the machine h. The starting time of operation ( h , j ) is yhj. The processing time of operation ( h , j ) is phj. The completion time of operation ( h , j ) is Chj. The completion time of the job j is Cj.
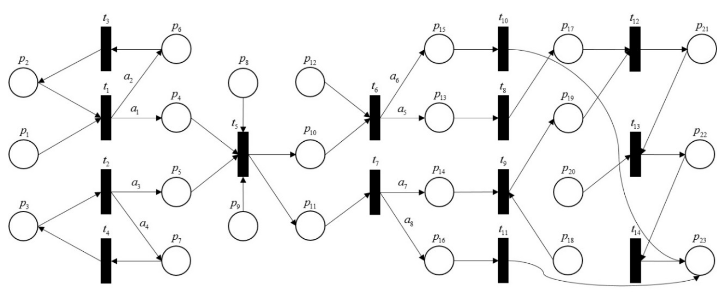
Figure 3. The timed colored Petri net model for self-adaptive collaborative production-logistics systems.
Based on the description of the production logistics problem, TCPN is used to model production and logistics in an FMS. The TCPN model of the self ‐ adaptive collaboration method is established as shown in Figure 3. Figure 3 shows the TCPN model of the self-adaptive collaboration method. This model refers to the basic cycle of production-logistics systems, which consists of twenty-three places and fourteen transitions.
Conditional statement expressions are assigned to the directed arcs a1, a2, a3, a4, a5, a6, a7, and a8. The cycle starts with checking workers and materials to be processed in production cells. Transition t1 denotes the check of workers while transition t2 denotes the check of materials. If the workers or materials are not ready, they will be requested.
SIMULATION RESULTS
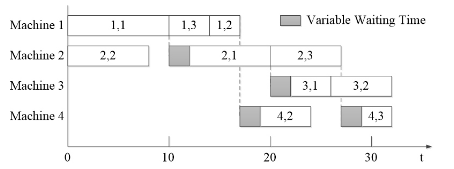
Figure 4. The feasible schedule plan
A feasible schedule plan is shown Figure 4. The initial time of the schedule was 0. The gray segment represented the variable waiting time between two continuous operations of the same job. In addition, two AGVs were added in the simulation experiment in order to investigate the collaborative relationship between production and logistics in a job shop.
Thus, the aforementioned job shop consisted of the following main components, namely a warehouse, four production cells, and two AGVs. The warehouse had an in-buffer and an out-buffer. Each production cell had a machine, an in-buffer, and an out-buffer. Machines and AGVs installed with sensors had the capability of perceiving status information in real time and making decisions based on the knowledge base and real-time information.
CONCLUSION
This work contributes to the study of production-logistics collaboration to improve economic and environmental performances of production-logistics systems. A TCPN simulation-based self-adaptive collaboration method for production-logistics systems is proposed. The method combines the schedule of token sequences in the timed colored Petri net with real-time status of key production and logistics equipment. The key equipment is made ‘smart’ to actively publish or request logistics tasks. An integrated framework based on cloud service platform is introduced to provide the foundations for self-adaptive collaboration of production-logistics systems. The capabilities of key equipment are packaged as cloud services to be published on the cloud services platform.
Computational experiments demonstrate that the proposed method is feasible and effective in reducing waiting time, makespan, and electricity consumption.A comparative study is implemented and the result indicates that the proposed method outperforms the event-driven method in improving the overall efficiency of the production-logistics systems and reducing electricity consumption. This work can be applied to other types of manufacturing systems to implement production-logistics collaboration. Future research will mainly focus on the following aspects. Other algorithms would be investigated and used to develop the production-logistics collaboration model and real-life data from the manufacturing environment would be used to verify the production-logistics collaboration model.
Source: Portland State University
Authors: Zhengang Guo | Yingfeng Zhang | Xibin Zhao | Xiaoyu Song