ABSTRACT
This article presents a new methodology for designing a hybrid control and acquisition system consisting of a 32-bit SoC microsystem connected via a direct Universal Serial Bus (USB) with a standard commercial off-the-shelf (COTS) component running the Android operating system. It is proposed to utilize it avoiding the use of an additional converter.
An Android-based component was chosen to explore the potential for a mobile, compact and energy efficient solution with easy to build user interfaces and easy wireless integration with other computer systems. This paper presents results of practical implementation and analysis of experimental real-time performance. It covers closed control loop time between the sensor/actuator module and the Android operating system as well as the real-time sensor data stream within such a system.
Some optimizations are proposed and their influence on real-time performance was investigated. The proposed methodology is intended for acquisition and control of mechatronic systems, especially mobile robots. It can be used in a wide range of control applications as well as embedded acquisition-recording devices, including energy quality measurements, smart-grids and medicine. It is demonstrated that the proposed methodology can be employed without developing specific device drivers. The latency achieved was less than 0.5 ms and the sensor data stream throughput was on the order of 750 KB/s (compared to 3 ms latency and 300 KB/s in traditional solutions).
RELATED WORK
The general concept of hybrid acquisition-control systems using mobile COTS devices can be found. The use of COTS-based hardware solutions is widely discussed and advocated while some application designing methodologies for demanding applications are described. COTS solutions have been suggested even for military and marine applications.
HARDWARE ARCHITECTURE
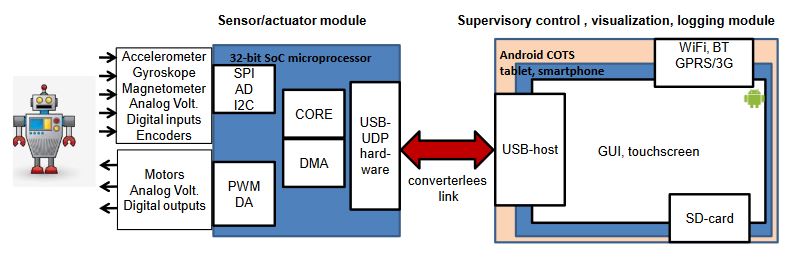
Figure 1. Proposed hardware architecture
The proposed hardware architecture is shown in Figure 1. This hybrid system consists of a sensor/actuator module and a control module. The sensor/actuator module involves a 32-bit system-on-chip (SoC) microprocessor responsible for performing analogue and digital measurements through external sensors (acceleration, orientation, touch, pressure, voltage, temperature, etc.). It can direct control mechatronic systems with proportional-integral-derivative (PID) type control, producing PWM, DA signals, and handling digital outputs.
SOFTWARE ARCHITECTURE
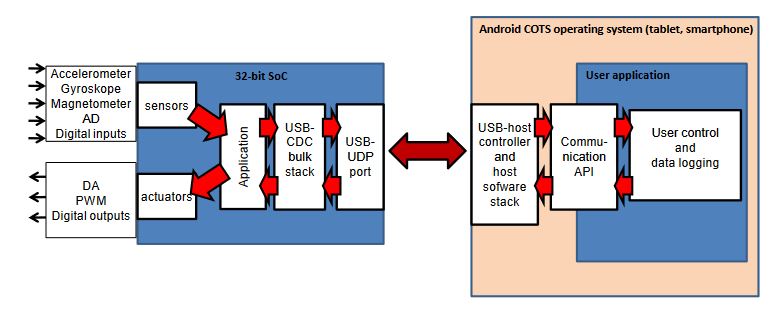
Figure 2. Software architecture of system’s key components
The microcontroller was programmed in C using a free GNU C compiler. USB interface handling accounted for 20% of the processor’s power, which means that it had 130 million instructions per second (MIPS) remaining for the application-related tasks involving signal processing and PID control. On the software side, the solution can be represented as several layers shown in a simplified form in Figure 2. The directions for sensor/actuator structure components module of SoC can be found.
EXPERIMENTAL RESULTS AND DISCUSSION
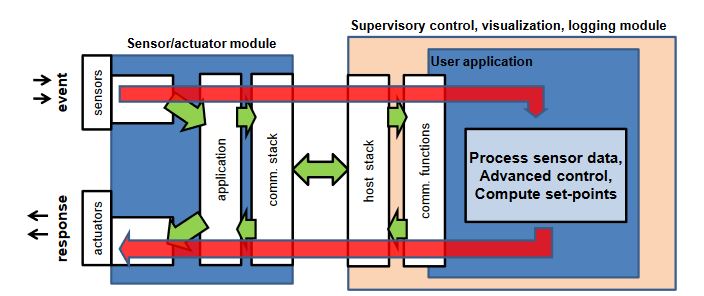
Figure 3. Closed control loop path
The proposed hybrid system was realized in the course of this study. The experimental testing program covered the real-time performance of closed control loop time (CCLT) and sensor data stream performance. It comprised the whole, integrated system along the data path: sensor module—USB interconnection—user Android application—USB interconnection—actuator module (see Figure 3).
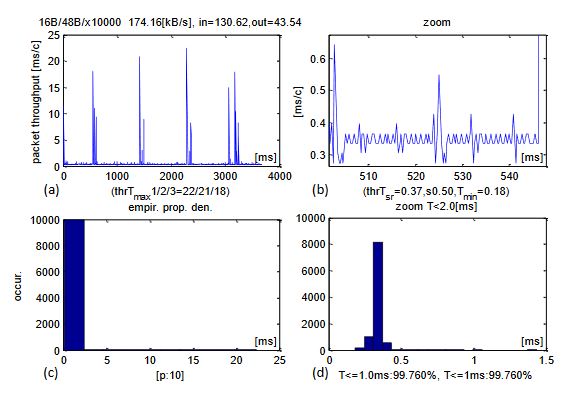
Figure 4. Experimental results of CCLT for packets
Detailed time performance of 48-B sized IN packets and their analysis are shown in Figure 4. This operational point is typical of control applications. The average CCLT was 370 μs. Most of the transactions were executed within 350–400 μs (Figure 4c, d) and 99.76% were carried out within 1 ms. The SD parameter was 600 μs and the minimum CCL Ts were contained within 230–280 μs.
CONCLUSIONS
This paper has presented a novel concept and the results of experimental real-time performance of closed control loop time in a hybrid acquisition-control solution. It consists of a 32-bit microsystem with an ARM core and a COTS tablet running the Android OS. A USB links the two components without any additional converters. Methods for software architecture optimization were presented as well as their experimentally measured performance.
The new concept shown in the paper was practically realized. It can be treated as a general framework. The experimental study shows that average closed control loop times (CCLTs) on the order of 370 μs in data exchange are feasible. Thereby, this paves the way towards control an d other real-time applications where the average response time required is less than 0.5 ms. Hence, the solution produces an average continuous sensor data stream on the order of 780 KB/s.
This allows an application in acquisition-recording devices, for example with sampling measurement data in eight sensor channels at the frequency of 45 kHz. Moreover, the solution implemented during the study was mainly intended to control mechatronic constructions but its areas of use go far beyond that. Indeed, the proposed solution has universal nature due to its compactness and low development cost that is reduced to a single-chip microsystem, a direct USB link and no additional specialised integrated systems or converters.
In terms of the software, typical programming libraries available from the operating system were employed without any need to develop specialised drivers for the device. The software can be adapted for applications in the areas of automation, robotics, personal medical devices, smart-grids and wind farms. A COTS device running Android lends itself to easy integration with other computer systems via wireless (Wi-Fi, Bluetooth) or mobile (GSM/3G) connectivity. The results obtained are relevant to other SoC microsystems with ARM, Cortex, MIPS, AVR32 cores or FPGA systems with a USB device port macrocell.
Source: University of Science
Author: Jacek Augustyn
>> More Wireless Projects based on Fpga for Engineering Students
>> Wireless Bluetooth Projects for Engineering Students
>> More Wireless Embedded Projects for Final Year Students
>> More Wireless Energy Projects for Final Year Students