ABSTRACT
The trend in the last few decades is that current unmanned aerial vehicles are completely made of composite materials rather than metallic, such as carbon-fiber or fiberglass composites. From the electromagnetic point of view, this fact forces engineers and scientists to assess how these materials may affect their radar response or their electronics in terms of electromagnetic compatibility. In order to evaluate this, electromagnetic characterization of different composite materials has become a need.
Several techniques exist to perform this characterization, all of them based on the utilization of different sensors for measuring different parameters. In this paper, an implementation of the metal-backed free-space technique, based on the employment of antenna probes, is utilized for the characterization of composite materials that belong to an actual drone.
Their extracted properties are compared with those given by a commercial solution, an open-ended coaxial probe (OECP). The discrepancies found between both techniques along with a further evaluation of the methodologies, including measurements with a split-cavity resonator, conclude that the implemented free-space technique provides more reliable results for this kind of composites than the OECP technique.
MATERIALS AND METHODS
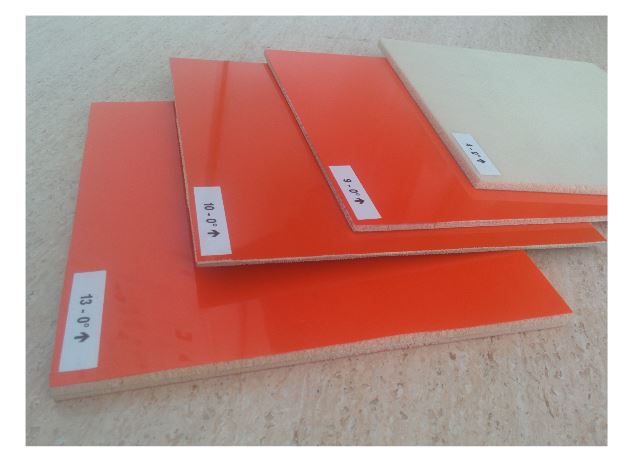
Figure 1. SCRAB-II materials under test
In this study, two sets of materials (a yellow and a white set, depending on the color of their sticker) are available. While the white set remains at INTA premises for different tests, the yellow set is frequently shared with other institutions. Each set consists of a number of 4 flat parallel faced samples of foam core fiberglass sandwich composite of dimensions 200 × 200 mm utilized in SCRAB-II. Note that fiberglass is non-magnetic ( μr = 1) and does not conduct electricity, therefore, only the complex permittivity will be characterized and its expected imaginary part will be very low. Each sample has its own thickness and a different number of composite layers as can be seen in Figure 1.
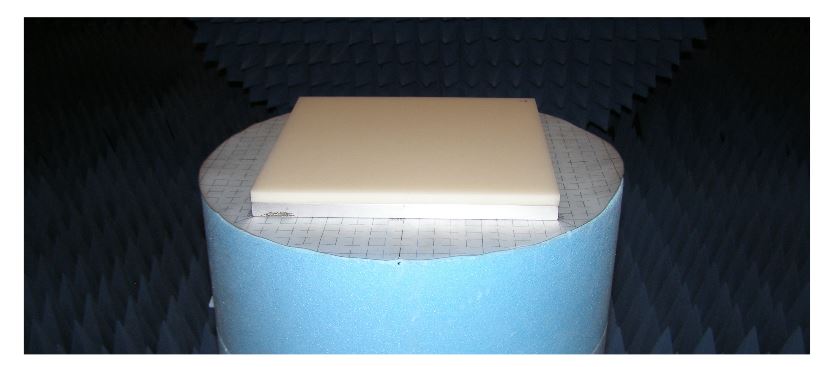
Figure 2. Metal-backed sample of Teflon
The measurement procedure for extracting the dielectric constants of the materials under test is discussed in the report by Ghodgaonkar et al and has been used in a variety of research papers. Basically, this procedure involves measuring the reflected signal from a flat material sample that has a perfectly conducting plate underneath, just as Figure 2 shows, where the reference material, a 10 mm thick slab of Teflon, is placed over a metal plate.
RESULTS AND DISCUSSION
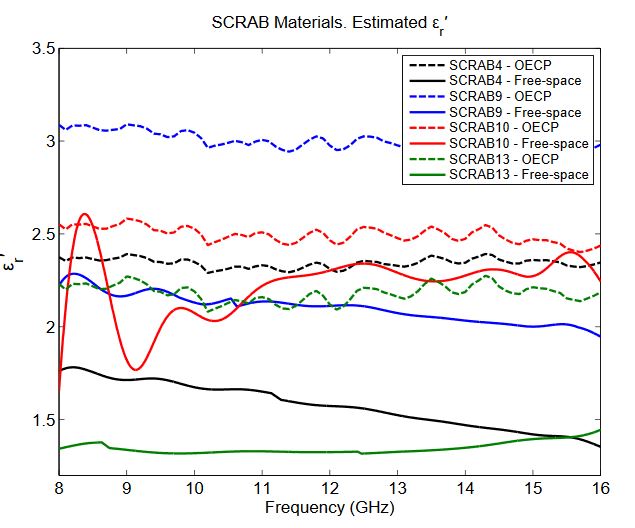
Figure 6. SCRAB-II materials estimated permittivity
The estimated complex permittivity for the four slabs of fiberglass material corresponding to the white set can be seen in Figure 6, where the results given by OECP and metal-backed free-space are compared. In Table 2, the mean permittivity along the frequency range for each material is summarized together with their thickness. As Figure 6 shows, the real part of the permittivity presents discrepancies between the values given by OECP and those estimated from the measurements in free-space.
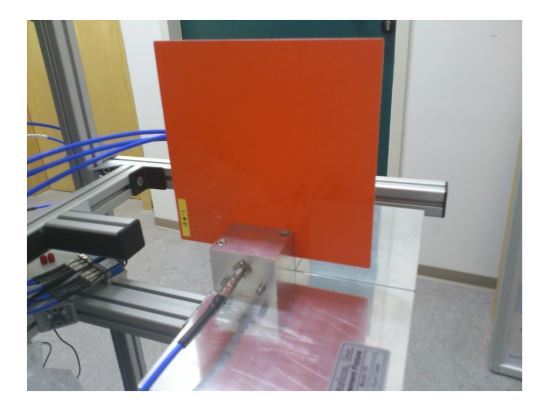
Figure 9. Measurement of a SCRAB-II slab material in a split cavity resonator
When a material is inserted into the cavity, it affects its resonant frequency and quality factor such that from their variation, the complex permittivity of the material can be calculated at specific frequencies. The measurement procedure is the same as the one explained in where a special mounting and measurement device with solid guidance structure is employed for the assembly of the materials under test inside the cavity. Figure 9 presents the measurement setup. Note that the measurements of these materials with this cavity only provide stable results up to 13 GHz due to the difficulties found in the proper determination of the resonant frequencies at higher frequencies.
CONCLUSIONS
A complete methodology to estimate the complex permittivity of composite fiberglass materials utilizing the metal-backed free-space technique along with the PSO algorithm has been provided. The aim of the paper was to prove that for radiated-fields-like applications (radar cross-section (RCS), electromagnetic compatibility under high intensity radiated fields (EMC-HIRF)…) and for these kinds of aeronautical low-loss materials, the metal-backed free-space technique is reliable enough.
To validate the results, the same materials have been measured with an OECP, but the agreement between the permittivity estimated by both techniques was not as expected. A further evaluation of two reference materials has shown that, due to the intrinsic inaccuracies of the OECP measurement procedure and the nature of the materials under test, the free-space approach returns more reliable results.
Bearing in mind the inhomogeneity of the considered materials, the proposed technique takes into account the whole sample, contrary to OECP, and is able to offer in just one measurement more reliable results for our purposes than other techniques presented (recall that OECP fails with material HiK500F). Another advantage of this methodology is the low manipulation required to prepare the test samples, which is particularly important for the special composition and fabrication process of the aeronautical composites.
To reinforce that metal-backed free-space is firm enough, an additional method has been applied, the split cavity resonator. The positive comparison of these last results have validated the free-space methodology explained along this paper for the extraction of permittivity, since the differences found in e between cavity and free-space are mainly due to small deviations in material thickness. Nevertheless, further investigation is needed in free-space for the accurate extraction of the imaginary part of the permittivity.
Authors: Patricia Lopez-Rodriguez | David Escot-Bocanegra | David Poyatos-Martínez | Frank Weinmann