ABSTRACT:
Controlling the power flow in transmission systems has recently gained increased interest. The difficulties of building new lines and the pressure of having a high utilization of existing assets, makes the flexibility of grid systems increasingly important.
This master thesis work investigates induction regulators as control devices for active power flow in a transmission system. A small change in angle of the rotor affects both the amplitude and the phase of the voltage. The magnetic coupling in the induction regulator can be controlled by changing the permeability of a thermo magnetic material such as gadolinium and can hence give a second independent controlling parameter.
An analytical model and calculations in the FEM software AceTriple C together with Matlab, is used to simulate the influence of the regulators connected to a simple grid in case1, a 400 kV scenario and case 2, a 45 kV scenario.
The analysis was carried out on a small transmission system consisting of two parallel transmission lines connected to source and load. The induction regulators are connected to one of the parallel transmission lines. The regulators modelled in case 1 must be able to control the active power flow in the regulated line to vary between 50 and 150 % of the original power flow through this line.
This shall be done over a range of 0 to 800 MW transmitted power. The regulators modelled in case 2 must be able to control the active power flow in the regulated line to vary between 0 and 30 MW, if this does not cause the power flow in the parallel line to exceed 30 MW.
This shall be done over a range of 0 to 50 MW transmitted power. The regulators are designed as small and inexpensive as possible while still fulfilling requirements regarding the active power flow controllability in the grid, current density in windings and maximum flux density in core and gap.
The results indicate that the size of the 400 kV solution has to be reduced to become competitive whereas for the 45 kV solution the relative difference to existing solution is smaller. Advantages with the proposed design over a phase shifting transformer are mainly a simpler winding scheme and the absence of a tap changer.
BACKGROUND
This chapter gives background to the different apparatus and phenomena used for the thesis work. In Chapter 3.1 the background to the induction regulator is given. Chapter 3.2 treats the power system and power flow equations. Permeability, and its influence on the magnetic flux density, is discussed in Chapter 3.3.
Induction regulator:
An induction machine is a rotating electromagnetic device. When used as a generator, the machine uses induction to transform mechanical power into electrical power. When used as a motor, electrical power transforms in to mechanical power. The machine consists of a non movable part, the stator, and a movable part, the rotor, both parts carrying windings.
The machine can be connected to single phase or poly-phase voltage, but are usable only for alternating current. Only the three- phase asynchronous machine used as a motor is considered here. The primary winding (stator or rotor) is connected to the grid. It produces an alternating magnetic flux density in the air gap between the stator and the rotor, which induces voltage in the secondary winding. The machine gets its magnetization power from the grid and the highest value of the flux density depends on the voltage in the grid.
Power System:
The current distribution in a transmission system depends on the impedance of the lines in the system. Imagine two parallel power lines with impedance za and zb,
Zj = rj + i.xj.
Permeability:
Permeability states how well magnetic flux is conducted in a material. Flux flows through a material with high permeability better than through a material with low permeability. The relation between permeability and magnetic flux is comparable to that of electric conductivity and current. Similar to how electric current tends to flow through materials with high conductivity; the magnetic flux tends to go through the material with the highest permeability.
METHODS
Grid model calculated in Matlab:
To analyse the behaviour of the power system when an induction regulator is connected, a Matlab program with a model of two parallel lines was written. In the model, one of the parallel lines is connected in series with the regulator.
CONCEPT
Thermo magnetic material:
Assume an induction machine as the voltage regulator mentioned above but instead of using an air gap, the gap between the primary and secondary windings mainly consists of a material where the permeability can be controlled and hence influence the magnetic coupling. One such material is the rare earth metal gadolinium, element number 64.
Motorformer:
The induction regulator must be useable at high voltages. This is not possible using conventional windings. The regulator will instead be winded using commercial available XLPE cables. This is a cylindrical cable which contains a solid dielectric layer of cross-linked polyethylene insulation, but unlike underground cables do not use any metallic shielding. The cylindrical shape causes the cable to produce a homogenous electrical field.
Connections:
The regulator is connected to the grid. The connection differs from the conventional induction regulator connection, by the use of a thermo magnetic material.
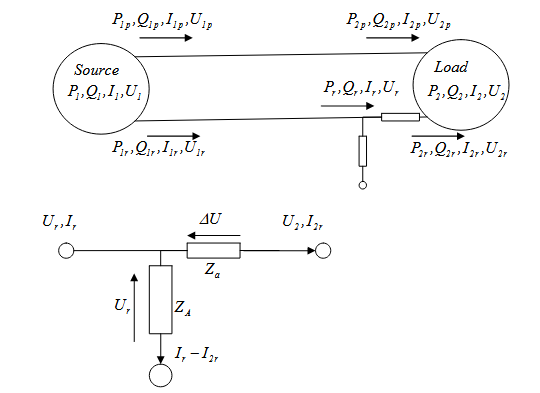
Regulator Shunt Connected to Line as in Case 1 and 2 Including Reference Directions of Voltages and Currents.
CASE 1
Requirements:
The regulator in the model is used to control the active power flow in two parallel lines connected to a source and a load. The source voltage in this case is 400 kV. For case 1 the induction regulator shall be connected to the transmission line . The line connected in series with the regulator is of length 60 km, while the line parallel to the regulator is of length 100 km in order to highlight power flow differences.
Results:
The results calculated for the induction regulator modelled with Python, using the parameter values from the optimization program, leaves margins to the critical limits stated in the regulator requirements. To optimize the regulator further, the different dimension parameters and their impact on the regulator result is examined.
CASE 2
Requirements:
The regulators in this chapter are modelled to control a smaller power flow then the regulators in case1. The regulators in this chapter are modelled to be of the same size as the Motorformer. The phase to phase voltage is 45 kV. The calculations assume Aluminium transmission cables. Cables can not transmit power the same distances as the over head lines used in. The length of the regulated line is set to 15 km and the length of the line in parallel to this is set to 25 km.
CONCLUSIONS
The case 1 regulators described in chapter six were not possible to simulate to be competitive to other existing transformers. The difference is, after the optimization work explained in this report, 50% heavier. A more thorough design needs to bee created to increase the size of the induction regulator further. Still, other benefits of the induction regulator exist in comparison to the phase shifting transformer.
The case 2 regulators where modelled as connected to a grid of much smaller voltage and could therefore be simulated as much smaller and still fulfil the requirements. They could possibly be competitive to existing transformers also other benefits of the induction regulator exists when compared to the phase shifting transformer.
The requirements regarding maximum flux density proved most difficult to fulfil. The size of the regulators where to a large extent decided by the maximum flux density in the gap and core. The maximum flux density in the gap increases considerable when increasing the permeability of the gadolinium placed in the gap. To be able to use the thermo magnetic properties of the material the regulators would therefore have to be increased in size.
The influence of the permeability proves to be limited when comparing the impedance matrixes modelled in IndReg to the analytical model of an ideal regulator. Most benefits and disadvantages connected to the use of a thermo magnetic material such as gadolinium can, for the modelled regulators, be connected to flux losses. These losses can be considerable reduced when actually constructing a regulator or a more detailed model.
Accordingly, the use of gadolinium gives small benefits. This can be seen in the analytical model where the permeability plays a minor role to the transmission matrix. The ratio between primary and secondary winding and the rotation angle of the secondary winding relatively the primary winding are the two things mainly controlling the induced voltage and therefore power flow.
FUTURE WORK
This thesis work can be a starting point of the analysis of an induction regulator for power flow control in transmission systems. There are several areas which need to be further investigated.
The first area concerns the regulator model. To evaluate the actual behaviour of the induction regulator the model should be refined. In a refined model the areas of high magnetic flux density and leakage flux can be reduced. The regulator can be designed to induce a more sinusoidal shaped voltage and the harmonics problem suppressed.
All the dimension parameters stated in the induction regulator model should be examined to minimize the size of the regulator. In this thesis work only the influence of two of them, L and gh, have been carefully examined.
The winding insulation should be examined to investigate possible winding properties solution. It is likely the current density of the windings can be increased and therefore the size of the regulator and need of Copper decreased.
This thesis work treats one single connection between induction regulator and grid. Alternative solutions to the connection need to be examined further. The regulation, and therefore the size of the induction regulator, is highly influenced by the connection between regulator and grid.
One alternative connection solutions not mentioned in this work has been somewhat examined, and it is not impossible that solution enables for the regulator to be decreased further. Alternative connections might also enable for the thermo magnetic material to be utilized better.
Another idea is as previously mentioned to extend the use of gadolinium to avoid mechanical movement when shifting the regulator. Instead of mechanically moving the regulator, a matrix made of gadolinium conductors can be created and used. By using different temperatures and cool the segments, the flux flows through a certain path in the matrix. This is equivalent to an actual change of the position of the primary windings relative the secondary windings in an induction regulator.
Source: Linkopings University
Author: Anna Guldbrand
>> 200+ Matlab Projects based on Control System for Final Year Students